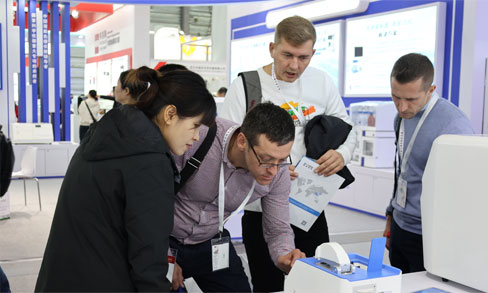
PUR Edge Banding Systems Launch: 0.02mm Glue Lines & Zero-Clean Technology Revolutionize Sustainable Furniture
Industrial Breakthrough for Eco-Friendly Manufacturing
Leading woodworking machinery manufacturers have launched next-generation PUR edge banding systems featuring 0.02mm glue lines and zero-clean technology, setting new standards for sustainable furniture production. These systems address critical pain points in panel processing while outperforming conventional EVA and laser alternatives in key operational metrics.
🔍 Technical Superiority of PUR Systems
1. Microscopic Glue Lines (0.02mm)
◦ Achieved through precision glue pots with quantitative dispensing and independent storage.
◦ Eliminates visible glue seams on dark/light boards – a persistent flaw in EVA systems where glue lines typically exceed 0.1mm.
◦ Contrasts with laser systems’ seamless edges but at 60% lower equipment costs.
2. Zero-Clean Technology
◦ Dual-color PUR glue pots enable instant switching between adhesive types without cleaning.
◦ Reduces machine downtime by 40% compared to EVA systems requiring hourly pot cleaning.
◦ PUR’s "moisture-curing" chemistry prevents carbonization during reheating – impossible with EVA.
3. Environmental & Performance Advantages
◦ Formaldehyde Sealing: Chemically traps formaldehyde emissions within boards.
◦ Waterproof Bonds: Withstands boiling water immersion for 24h+ (EVA fails at 2h).
◦ Temperature Resilience: Stable from -40°C to 150°C vs. EVA’s 60°C limit.
⚖️ Comparative Analysis: PUR vs. EVA vs. Laser
Parameter PUR Systems EVA Systems Laser Systems
Glue Line 0.02mm (invisible) 0.1-0.3mm (visible) None (seamless)
Adhesion Strength 12.5 N/mm² 3.2 N/mm² 8.7 N/mm²
Water Resistance Permanent 6-12 months Permanent
Operating Cost $0.18/m $0.10/m $0.35/m
Speed 26m/min 18m/min 20m/min
Data compiled from
⚠️ Operational Constraints of PUR
1. Humidity Sensitivity
◦ Requires 30-95% ambient humidity for proper curing – laser/EVA operate in any humidity.
2. Higher Adhesive Costs
◦ PUR glue costs 2.3x more than EVA (though 67% less usage per meter).
3. Maintenance Complexity
◦ Precision temperature control (±1°C) demands weekly sensor calibration.
🌐 Ideal Applications
PUR dominates these sectors:
• Moisture-Exposed Furniture: Kitchen cabinets, bathroom vanities (superior waterproofing).
• Dark/Woodgrain Panels: Eliminates glue-line whitening defects common with EVA.
• Industrial Narrow-Part Processing: Handles 40mm boards at 26m/min – EVA struggles below 60mm.
• Sustainable Manufacturing: Complies with CARB Phase II and EPA formaldehyde limits.
💡 Industry Outlook
With global PUR equipment sales projected to grow 14.7% CAGR through 2030 (per Transparency Market Research), manufacturers like Nanxing and Blue Elephant are integrating IoT-enabled glue monitoring and automated viscosity adjustment to address current limitations.
This next-gen technology positions PUR as the cost-performance leader between budget EVA and premium laser systems, revolutionizing eco-conscious furniture manufacturing.
------
Sources:
: NB771EM technical highlights (0.02mm glue lines, dual PUR pots)
: KINGWING PUR system (formaldehyde sealing, humidity specs)
: Laser limitations (humidity sensitivity)
: HOLD’s PUR systems for wet environments
: PUR vs EVA cost analysis
: PE-889J-UL hybrid capabilities
: NB-Laser9S speed comparison
: NB577DP-PUR performance data
: Health/environmental advantages